有限元分析在薄壁注塑模具設(shè)計(jì)中的應(yīng)用
2017-01-23 by:CAE仿真在線 來源:互聯(lián)網(wǎng)
11 前言
“薄壁”通常由壁厚少于1mm的輕便電子制件所定義的。對大的汽車部件來說,“薄”可以是2mm。目前,生產(chǎn)小尺寸、高精度、構(gòu)造復(fù)雜的薄壁制件已經(jīng)成為 注塑加工面臨的主要挑戰(zhàn)。由于快速充模和高壓能以高速將熔融的熱塑性材料注入模腔中,從而防止了澆口冷固。因此,注塑速度和壓力成為確保薄壁注塑成功的關(guān) 鍵因素。當(dāng)前,一個厚度小于2 mm的電子制件,充模時間通常不超過0.5秒,而注塑壓力往往高于50MPa 。
為了縮短產(chǎn)品注塑成型周期,降低模具原材料成本,減少模具厚度已經(jīng)成為設(shè)計(jì)人員采用的主要手段。但過薄的模具在經(jīng)受注塑高壓的沖擊下會引起模板彎曲過大, 導(dǎo)致注塑制件不合格。面對這一矛盾,企業(yè)往往僅能依靠設(shè)計(jì)人員的經(jīng)驗(yàn),多次試模、修模,不斷重復(fù),直至注塑出合格的試樣。這樣對企業(yè)人力、物力資源都是很 大的浪費(fèi)。而有限元分析(FEA)技術(shù)彌補(bǔ)了模具設(shè)計(jì)過程中依靠經(jīng)驗(yàn)試制所帶來的定性不定量的不足,它可以幫助技術(shù)人員在模具設(shè)計(jì)初期階段,及時發(fā)現(xiàn)問題 并加以改進(jìn),從而提高生產(chǎn)效率,減少生產(chǎn)成本。目前,FEA在模具行業(yè)受到了越來越廣泛的重視。
本文借助大型有限元工程軟件ANSYS對某款薄壁注塑模具進(jìn)行應(yīng)力、應(yīng)變分析和尺寸優(yōu)化。首先將模具整體幾何模型導(dǎo)入到ANSYS 中。然后,考慮模具的實(shí)際工作載荷和邊界約束,對其施加位移和壓力邊界條件,以模擬其真實(shí)的注塑環(huán)境,并對整個模具進(jìn)行網(wǎng)格剖分和應(yīng)力、應(yīng)變分析。最后, 尺寸優(yōu)化設(shè)計(jì)為模具改進(jìn)提出了參考方案。
22 有限元建模
2.1 幾何模型導(dǎo)入
圖1 所示是廠家提供的在某款注塑模具的幾何模型,整個模具是由面板、底板、方鐵、公模、公模鑲件、母模鑲件和母模7 個主要部分組成,熔融塑料被注塑機(jī)高壓射入澆口,流經(jīng)面板、公模,進(jìn)入由公模和母模鑲件所形成的內(nèi)腔中,經(jīng)保壓成形生成成品制件。
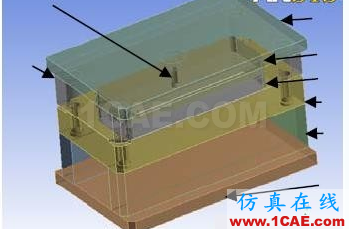
(1 底板;2 方鐵;3 公模;4 公模鑲件;5 母模鑲件;6 母模;7 面板;8 澆口)
幾何模型導(dǎo)入到ANSYS 中是整個仿真分析的基礎(chǔ),利用ANSYS 與UG 的雙向互導(dǎo)功能,可以在UG 的設(shè)計(jì)環(huán)境中直接激活A(yù)NSYS 并導(dǎo)入到ANSYS 分析環(huán)境,這就實(shí)現(xiàn)了從設(shè)計(jì)到分析的無縫接合,導(dǎo)入到ANSYS 的模型保留了原UG 模型的所有特征而沒有任何丟失(見圖1)。另外,ANSYS 在導(dǎo)入模型的過程中,自動識別并且建立了各連接部件之間的接觸關(guān)系,由此大大簡化了接觸關(guān)系的定義工作,提高了分析效率。
2.2 初始條件設(shè)置
1)模腔壓力和鎖模力
模腔壓力P 主要受下面5 個因素影響:澆口的數(shù)目和位置、澆口的尺寸、制品的壁厚、使用塑料的粘度特性和注塑速度。根據(jù)文獻(xiàn)
P= P0×K=39×1.4= 54.6MPa (1)
注塑件投影面積數(shù)值:S = 6984.07mm2
該注塑模具工作所需要的最小鎖模力:
F=P×S=54.6×106×6984.07×10.6 =381.33KN (2)
2)模腔壓力加載時間歷程
通過載荷時間歷程的施加方式,來模擬填充到保壓階段的應(yīng)力變化,即模腔壓力由注塑開始的0MPa,上升到保壓階段開始的最高壓力,然后在保壓階段下降到最大壓力的80%,最后卸載至0MPa ,這稱為一次加載過程,如圖2 所示。
圖2 模腔壓力加載時間歷程
綜上分析,在面板上施加鎖模力,大小381.33KN ,方向由面板指向公模。在模腔的內(nèi)表面施加最大注塑壓力,大小54.6MPa ,方向垂直于模腔內(nèi)表面,底板上使用固定約束,以模擬模具在注塑階段到保壓階段中的工作情況。所施加的邊界條件如圖3 所示。
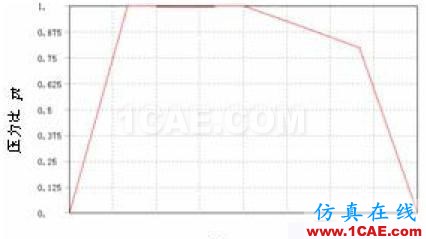
2.3 材料參數(shù)
面板、底板、方鐵、公模和母模的材料為普通碳素鋼S45C
2.4 模型的網(wǎng)格化
該注塑模具模型共劃分了284954單元,總節(jié)點(diǎn)數(shù)是478202,如圖4所示。具體網(wǎng)格劃分方式與單元尺寸設(shè)定如下:
1) 面板,底板和方鐵4 個部件,使用六面體占優(yōu)的網(wǎng)格劃分方式,單元邊長尺寸為12.5 mm ,共劃分4852 單元,25221 節(jié)點(diǎn);
2) 公模和母模2 個部件,使用六面體占優(yōu)的網(wǎng)格劃分方式,單元邊長尺寸為8 mm,共劃分81771 單元,134523 節(jié)點(diǎn);
3) 公模鑲件和母模鑲件2 個部件整體上使用六面體占優(yōu)的網(wǎng)格劃分方式,單元邊長尺寸為8 mm;同時,為了捕捉模腔內(nèi)的細(xì)節(jié),再選擇模腔內(nèi)表面102 個面,使用全四面體的網(wǎng)格劃分方式,單元邊長尺寸為1.2 mm ,最共劃分198331 單元,318458 節(jié)點(diǎn),如圖5所示。
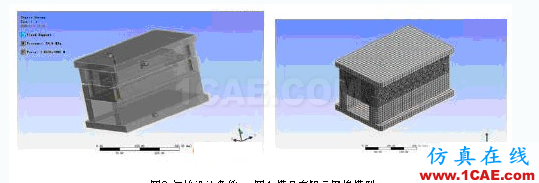
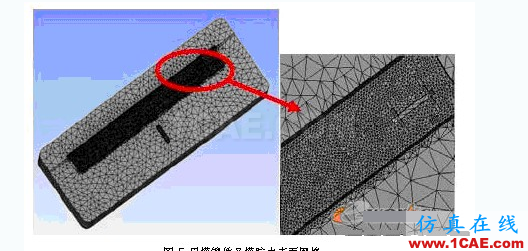
33 模具剛度和強(qiáng)度計(jì)算結(jié)果
通過計(jì)算結(jié)果的云圖顏色深淺就可以判斷變形和應(yīng)力的大小,通過最大/最小值圖標(biāo)可以方便地判斷最大/最小應(yīng)力、應(yīng)變的位置。同時,在計(jì)算結(jié)果的后處理中, 可以通過將應(yīng)力、應(yīng)變結(jié)果做成動畫,更加直觀地顯示計(jì)算結(jié)果,方便設(shè)計(jì)人員確定問題所在。計(jì)算所得模具整體最大變形為0.0199mm,發(fā)生位置為公模/ 母模鑲件模腔表面(如圖6所示);最大等效主應(yīng)力(Von Mises 應(yīng)力)為302MPa ,發(fā)生位置為母模鑲件模腔表面;面板與公模之間的最大壓力為67.4MPa ,方鐵與底板、母模之間的壓力最大為102MPa 。上述指標(biāo)均符合設(shè)計(jì)要求,即“保證塑件加工精度在0.01mm~0.03mm 之間”,最大等效應(yīng)力小于材料屈服強(qiáng)度(826MPa )。
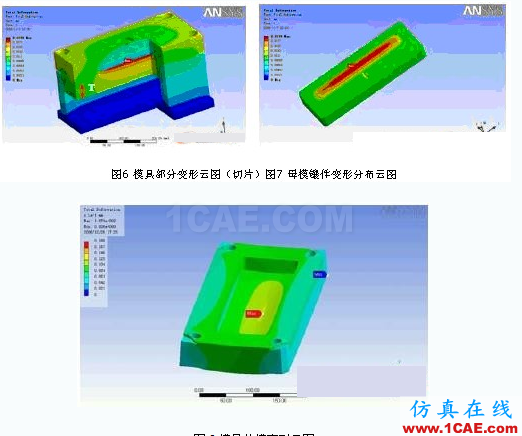
44 模具優(yōu)化設(shè)計(jì)
為了改進(jìn)模具設(shè)計(jì),在模具整體變形和應(yīng)力值不超過設(shè)計(jì)要求的情況下,盡可能的減少材料,對不同厚度的公模進(jìn)行了對比計(jì)算。當(dāng)公模的厚度(圖6 所示尺寸T)變薄2mm 時,有限元分析的結(jié)果如圖8 所示。從圖中可以看到公模最大變形由原來的0.011mm 增加為0.019mm ,最大變形發(fā)生的位置在公模底面中心位置(圖8,MAX 處)。公模厚度減少2mm ,模具變形不大,依然滿足“保證塑件加工精度在0.01mm~0.03mm 之間”的設(shè)計(jì)要求。
55 結(jié)論
借助ANSYS 結(jié)構(gòu)靜力學(xué)分析功能,對某型號注塑模具的應(yīng)力應(yīng)變分析,確定其在特定工況下(鎖模力為381.33KN ,注塑壓力為54.6MPa )模具的整體變形及應(yīng)力分布,校核模具在工作狀態(tài)下的結(jié)構(gòu)強(qiáng)度。獲得以下結(jié)論:
1)利用ANSYS 和UG 間的接口,能夠?qū)⒆⑺苣>吣P蛯?dǎo)入到ANSYS 分析環(huán)境中,并且能夠自動的建立和識別零部件間的接觸關(guān)系,提高了分析效率;
2)整個模具的鑲件部分變形最大值為0.0199mm ,位置在母模鑲件模腔內(nèi)表面上,保證了該注塑模具加工塑件的精度在0.01mm~0.03mm 之間,故可以認(rèn)為該模具結(jié)構(gòu)設(shè)計(jì)比較合理;
3)整個模具的鑲件部分等效應(yīng)力分布比較均勻,雖然局部最大應(yīng)力達(dá)到302MPa ,考慮到該部分使用的模具鋼2738 ,并未超出其屈服強(qiáng)度(826MPa),故可以認(rèn)為這個結(jié)構(gòu)設(shè)計(jì)比較合理。
4)模具局部最大應(yīng)力值隨之鎖模力和注塑壓力的增大而增大,采用ANSYS 多工況分析,計(jì)算得到導(dǎo)致模具發(fā)生塑性應(yīng)變的最大鎖模力為1042KN ,最大注塑壓力為149MPa 。
5)根據(jù)不同尺寸的模具,做了優(yōu)化分析。在滿足工作要求的情況下,得到最優(yōu)的模具尺寸,即公模厚度減少2mm ,從而節(jié)省了模具材料和制造成本。
相關(guān)標(biāo)簽搜索:有限元分析在薄壁注塑模具設(shè)計(jì)中的應(yīng)用 Ansys有限元培訓(xùn) Ansys workbench培訓(xùn) ansys視頻教程 ansys workbench教程 ansys APDL經(jīng)典教程 ansys資料下載 ansys技術(shù)咨詢 ansys基礎(chǔ)知識 ansys代做 Fluent、CFX流體分析 HFSS電磁分析 Abaqus培訓(xùn)